The Power of Respiratory Gas Analysis To Optimize Biopharmaceutical Processes
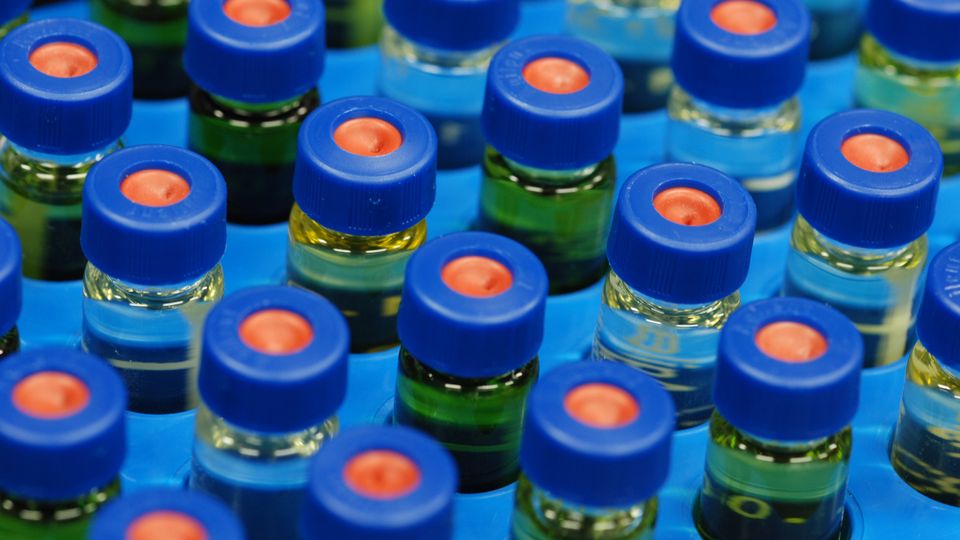
Complete the form below to unlock access to ALL audio articles.
Fermentation and mammalian cell culture are critical processes for the production of many drug products including therapeutic monoclonal antibodies and vaccines, and underpin many of the recent advances in cell and gene therapy. The cell culture and its environment must be carefully monitored to meet the tight controls on biopharmaceutical manufacturing, as well as to ensure high yields and avoid unwanted by-products. Respiratory gas analysis can be used to characterize the behavior and productivity of the cells by monitoring the gases being fed into, and produced by, a culture during incubation. Online process mass spectrometry is a technique for continuous respiratory gas analysis that can fit within the regulatory frameworks for process monitoring, making it a useful tool for improving process insights and driving better outcomes during cell culture or fermentation.
The steps of PAT implementation
Process analytical technology (PAT) uses continuous monitoring to gain a better understanding of how processes work through real-time measurements. The data generated can then be used to improve process control and outcomes. Within the biopharmaceutical industry, these outcomes may include improving product quality, ensuring regulatory compliance, reducing processing time, or accelerating the development of new products. PAT is a multi-step process, beginning with understanding the critical quality attributes (CQAs) for the process that needs to be maintained/improved, then identifying which critical process parameters (CPPs) impact those CQAs and, eventually, continuous monitoring and control of CPPs to improve process outcomes.
Figure 1: Implementation steps for PAT.
PAT of biopharmaceutical fermentation
There are many types of PAT used in pharmaceutical development and manufacturing, depending on the type of workflow that is being monitored. Fermentation is a complicated process that requires careful control of the environment, as well as monitoring the state of the culture, to increase yields and avoid unwanted by-products. During biopharma fermentation, sparge gases provide oxygen, aid the control of pH and temperature, and promote efficient mixing within the bioreactor. This process involves the careful regulation of various gases – including oxygen, carbon dioxide and nitrogen – to create an optimal environment for the growth and metabolism of cells. Fermentation also generates off-gases, or outlet gases, such as carbon dioxide and other metabolic by-products. Proper gas flow management to remove these off-gases – while minimizing any potential loss of valuable volatile compounds – is essential, as accumulation can inhibit cell growth and product formation.
Online monitoring of both sparge and outlet gases can be used to calculate the respiratory quotient (RQ) – the rate of oxygen consumption and carbon dioxide evolution. Knowing the RQ is essential to understand the health of the culture, indicating both the metabolic efficiency and the type of nutrients being consumed. Precise evaluation of the concentrations of a bioreactor’s inlet and outlet gases – including volatile gases – provides an ideal approach to accurately track a culture’s growth kinetics and substrate consumption in a non-invasive manner, without compromising the sterility of the environment. This data provides invaluable insights to help optimize processes, feed times and the start of induction, as well as to determine the ideal time to stop fermentation for maximum viable cell mass. Real-time gas analysis also provides opportunities to identify contamination prior to inoculation, as well as to detect unwanted by-products and the onset of poisoning. These factors improve overall manufacturing efficiency, reduce over-processing and waste, and contribute to higher biopharmaceutical yields and profits.
Online process magnetic sector mass spectrometry
Mass spectrometry (MS) is a relatively simple and non-invasive way to analyze the gases involved in fermentation processes. This technique does not require sample collection or the use of sensors that are placed inside the sterile fermentation area, helping to prevent contamination. MS platforms also offer more flexibility than alternative gas analyzers, because their analytical methods are primarily defined in the software, allowing the analysis of a wide range of sample streams with different compositions. Furthermore, MS is often quicker, more accurate and more versatile than other techniques, and the instruments are self-calibrating with very low maintenance requirements, reducing downtime and allowing continuous use.
Most mass spectrometry workflows consist of the same three key steps – ionization, mass separation and detection – but magnetic sector MS has emerged as a preferred method for fermentation monitoring. This approach uses a variable magnetic field to separate charged particles and has now been employed successfully by many of the world’s leading biotechnology and pharmaceutical companies. Magnetic sector MS uses hot filament electron ionization to produce positively charged ions from the sample gas. This is followed by mass separation, where the positively charged ions are accelerated with high energy into a scanning magnetic sector and deflected according to their mass and charge. These deflected ions then enter the detector, where the signal generated by the ions is measured, with the number of ions from each gas molecule being directly proportional to the signal generated at the detector.
This technique offers numerous advantages over quadrupole MS – including higher linearity, accuracy and precision. It also uses a high ion acceleration voltage to produce high-energy ions, reducing its susceptibility to scattering by contamination from residual molecules in the vacuum system. This enables the analyzer to achieve excellent stability and continuously operate for long periods. Another benefit of magnetic sector MS is that instruments are less influenced by surface charging effects – due to imperfect electrode surfaces – which can result in misalignment or drift in the mass axis. With magnetic sector MS, the signal intensity at any specific mass position appears as a flat-topped peak, removing the need to measure exactly the middle of the peak, and making the system intrinsically fault tolerant. This allows magnetic sector MS systems to have long intervals between calibrations, making them extremely beneficial for prolonged fermentation processes, which can last days or even weeks.
Conclusion
PAT is critical in the biopharmaceutical industry to meet regulatory requirements and ensure effective process control. Real-time gas analysis is particularly useful for monitoring fermentation and cell culture, enhanced by the development of innovative and intuitive MS devices. These systems offer a simple and non-invasive way to analyze the gases involved in the workflow, and don’t require sample collection or the use of sensors placed inside the sterile fermentation area, eliminating a potential source of contamination. Crucially, magnetic sector MS provides essential data – such as the RQ – to allow operators to make informed decisions about feed times and when to halt fermentation. This helps to significantly boost yields and profits, while producing more consistent biotherapeutic products.